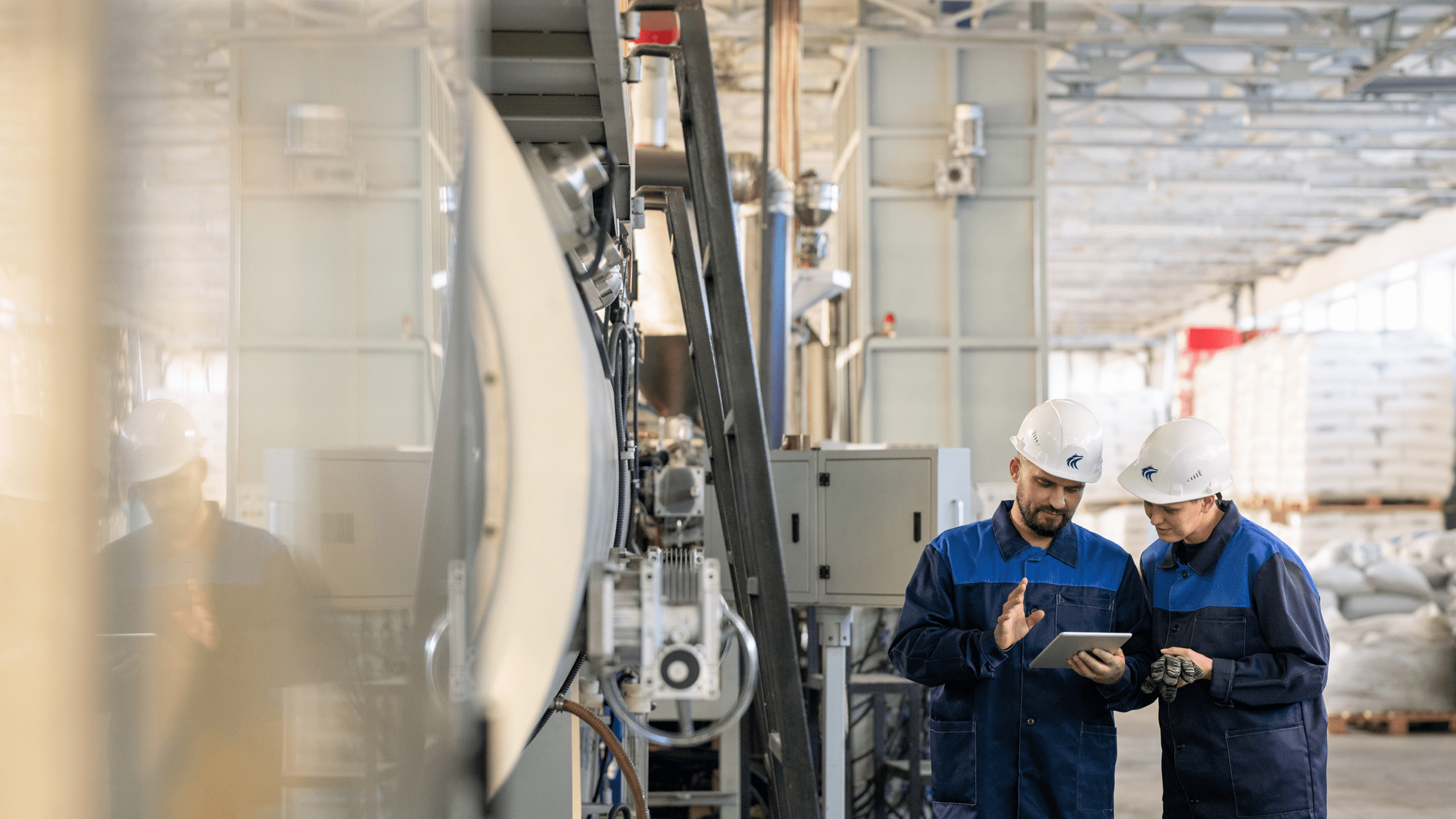
The Easy Button for Improving Asset Performance
Including lube oil flushing, fluid reconditioning, asset monitoring and more.
Embedded Technician Program
Our service strategy at Blue Wolf includes an Embedded Technician Program that places local plant technicians inside
customer facilities to maintain equipment, manage lube oil flushing, run fluid reconditioning services programs, recommend service schedules, and execute pre-commissioning and plant reliability service programs. Local technicians are trained through BW’s program and on the specific customer site culture and practices.
This program allows Blue Wolf to maintain a customer focus and price point well below sporadic contract labor and increase efficiencies with embedded technicians understanding site geography and requirements. Current Programs include MLA & MLT trained personnel to perform services including:
- On site reclamation of hydraulic fluids and/or coolants
- Air Breather supply and replacement
- Oil Filter supply and replacement
- Oil Sampling
- Oil Sample Report Review
- In-line lube oil flushing, filtration, dehydration, and varnish mitigation
- Documentation, maintenance reporting, cost savings analysis
Below is an overview of how this program works:
Step 1: Identify Opportunities
The Blue Wolf team identifies customers who meet or more of the following criteria:
- Currently have a lubricant reclaim program where they are reclaiming 4K gallons through a tote program or trucking (as needed)
- Are selling/disposing their used oil through their waste provider (ex. Safety-Kleen or Clean Harbors)
- Have a need for service equipment to be provided (or supported)
- Regularly need samples pulled, filters and breathers changed, or tanks/reservoirs cleaned
Step 2: Establish a Scope of Work
Once a customer with these needs is identified, Blue Wolf performs a site walk-down to gather information,
including:
- Oil reclamation information—Type of oil & monthly volume; Full-time or part-time labor needed; Footprint of work area and collection point of used oil
- Sampling/breather/filter needs—Units that will be sampled; Frequency needed; Days/hours of accessibility to plant
- Equipment needs—Sizing the equipment; Establishing servicing intervals; Footprint of area available; List of pieces that need to be provided vs. serviced
- Reservoir/Tank specifications—Identify oil used; Manpower & equipment required to accomplish task; Current and needed service intervals
Step 3: Recruit Local Technician
After a customer scope of work is outlined, this information will be used to build a recruiting ad for a local
technician. The ad will be based on:
- The needs/skills needed from the scope of work that will be required
- Additional certifications that may be required to get onsite such as; TWIC Card-Basic Plus-Hazwoper-Training-MSHA.
- Language requirements. Some technicians may need to be bilingual to successfully interact with plant staff
- What hours technician will be required to work. (ex.1st-2nd-3rd shifts, weekend or rotating shifts).
- Once the description is written and approved, the job will be posted internally for 1-2 weeks for internal candidates willing to relocate. After two weeks, the job will be posted publicly
Step 4: Technician Hiring
Qualified candidates will be interviewed. The interview process consists of:
- Conducting a working interview with candidate(s) at a similar job site to help them better grasp the basic concepts and see if they understand the daily functions and working conditions of the position
- Once a top candidate is selected, they will pass through a screening process that includes:
- Verifying past employment and performance
- Background check
- Drug screening
- Passing candidates will be presented an offer letter
- A start date is established
Step 5: Training Program
New technicians will be trained at a facility where we already have an establish program with a senior
technician for one week. The senior technician with train the new technician on:
- Proper equipment handling
- Correct sampling methods
- How to establish a relationship with the plant contact
- How to build site-specific SOP guidelines for the new site
- All on-site procedures and safety expectations of Blue Wolf employees
Step 6: On-Site Procedures for Lube Oil Flushing, Fluid Reconditioning Services and More
After the training week, new technicians will be deployed to their local client site. The first task once on-site
will be to build a site-specific SOP program for review by the Blue Wolf team. After the SOP is approved, a daily
EOD (End of Day) report will be created to show daily progress at site that will be sent out to plant contact
and the new hire direct report. The daily report will be tracked to look for trends or areas of improvements
and a monthly report will follow.
How Can We Help?
Get A Quote for Turnaround Services, Additional Information, or Technical Help by Reaching Out: