Synopsis
Hydrate ice on a plate heat exchanger was creating unwanted resistance and a pressure drop, impacting ethylene production. Blue Wolf was able to melt the ice under live conditions – avoiding shutdown – using our proprietary Liquid-Injection-Lancer (LNL). This saved the facility an estimated $18 million in avoided shutdown and gained $700,000/day in improved output.
A large petrochemical company experienced a reduction in ethylene production at their facility in Corpus Christi, Texas. Hydrate icing had formed in a very large plate heat exchanger (cold-box) which created an unwanted resistance and pressure drop across the heat exchanger (Delta P).
Knowing that Blue Wolf has online cleaning capabilities that avoid shutting down critical equipment, the engineering team reached out to Blue Wolf to discuss possible solutions. It was quickly decided that a large volume stream of atomized methanol or iso-propylene spray could melt the large amounts of ice in the exchanger under live conditions.
The only possible entry point into the live system was a one-inch valve at a strainer upstream from the ethylene cold box. Blue Wolf built a complete mock-up of the strainer system within 3 weeks, and demonstrated to the client our entry procedure and atomizing 80GPM fluid using one of Blue Wolf’s 750 horsepower pumping systems.
Solution
Blue Wolf’s engineering team provided and delivered a fully engineered service package providing all procedures, safety systems and execution of the “live” cleaning within the shortest possible time. Our project preparation for using the Liquid-Lancing-Injection (LIL) included::
- Design a hydraulic system that enters the 500 psi pressurized “live” ethylene stream at minus 30 degree temperature
- Develop an atomization nozzle that can spray 80 gpm methanol at 10,000 psi working pressure while being attached to the hydraulic system.
- Convert a 750 horsepower Blue Wolf system from water to methanol pumping
- Build a remote control and monitoring system so the project can be performed from 300 feet away
- Build a mock-up of the client’s strainer and one inch connection valve for testing purposes
- Help client to develop a project risk management plan for the ethylene unit
Results
he “Liquid-Injection-Lancer” (LIL) system successfully injected atomized methanol at 80GPM flow into the live ethylene production stream of the plant. All work was performed remotely from a Blue Wolf video van so no personnel had to be close to the minus 30 degree production system.
The total active project time included 15 injections with 15 minutes each with a total of 17,800 gallons of methanol pumped by Blue Wolf. Including all preparation and safety meetings the injections were performed within a four-day time period during day-shift only.
$700,000/day in Saved Production
The icing that used to cause a 37% blockage was reduced down to 23% blockage. This reduction allowed ethylene production to return to normal levels and save nearly $700,000/day in lost ethylene production that would have continued without the blockage reduction.
Avoided $18 Million in Unplanned Shutdown
This procedure was performed live without shutdown. The reduction in ice was enough for the plant to continue to run without noticeable production loss until the next planned shut-down in 2023. This saved the company an estimated $18 million for a 2-3 week unplanned shutdown that never happened.
Fully Demonstrated Produced Ensured Safety
The complete system mock-up and procedure walk-through at Blue Wolf’s facility ensured the procedure was fully planned, safe, and both teams were fully prepared before the cleaning ever started.
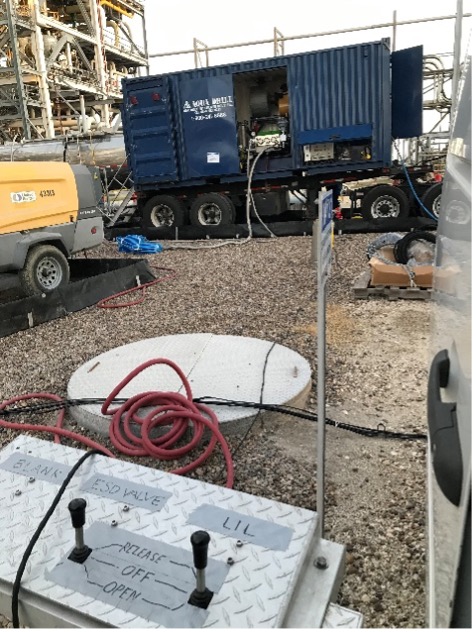
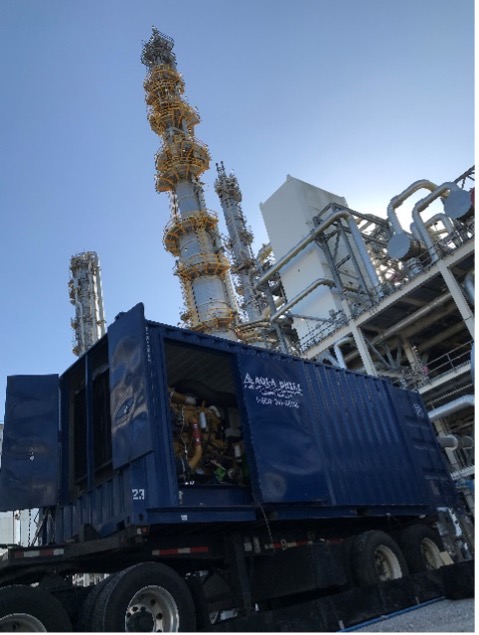
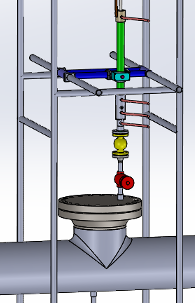
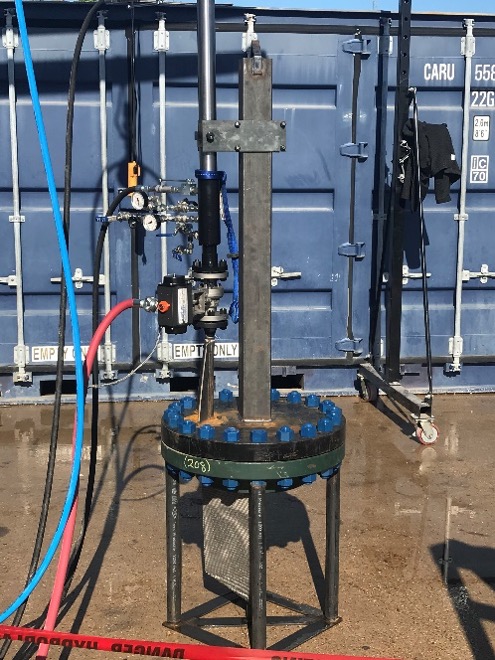
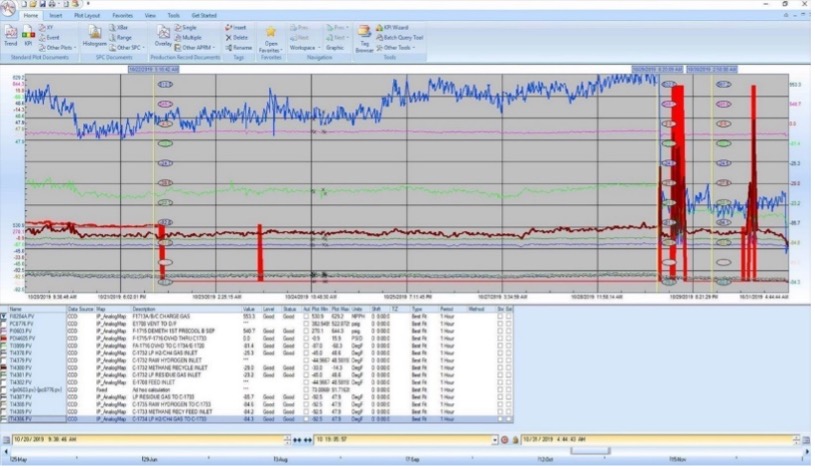
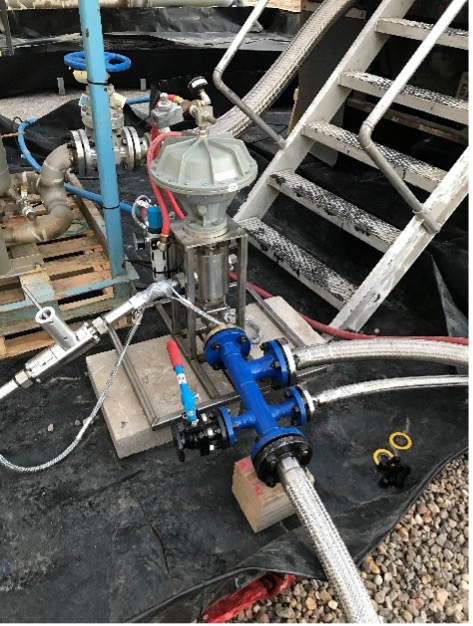